CAN is a message-based protocol, designed specifically for automotive applications and as of now, for any avionics
equipment in safety critical applications. The CAN Interface module is a dedicated interface which enables data communication for ARINC825 application layer. It allows a system with an embedded CAN bus to transmit information quickly and surely.
The hardware item only covers digital layers of the CAN Protocol bus architecture.
The D002_ARINC825 matches major needs of any critical application and mainly those requiring a DO-254 DAL-A compliance in the aerospace area.
CAN ARINC 825 - DO-254
Overview
Key Features
- IP developed according to DO-254/ED-80 guidance. Compliant DAL A.
- Compliant with ARINC825-1 Specification. May 10, 2010.
- Compliant with CAN 2.0 Specification (v 2.0) published by Bosh (part A and part B).
- Able to recover from SEU (self healing feature) and to report any detected errors thanks to its embedded reliability features.
- Support Transceiver ISO1050 from Texas Instrument and Philips TJA1040 with Standby mode.
Benefits
- The CAN IP Core has been implemented in Microchip FPGA in a DAL-A application for a civil aircraft. This IP Core has been certified DAL-B by official certification authorities.
Block Diagram
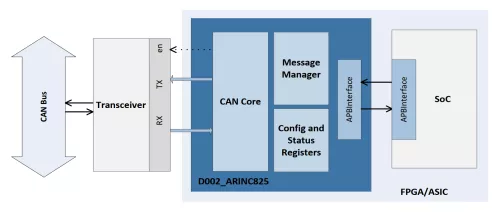
Applications
- The CAN IP Core is perfectly adapted for civil aerospace application.
Deliverables
- Technology independent, VHDL or Verilog RTL source code compliant with SILKAN s design standard.
- SystemVerilog verification test-benches with 100% code coverage and functional requirement coverage.
- Reference Design as integration example (i.e Dry Run).
- SILKAN s support includes technical integration, DO-254 integration and certification phases.
- IP Datasheet and Customer Requirement Specification (CRS) document.
- Encrypted version available immediately.
- Final delivery received five months after committed HRD.
Technical Specifications
Short description
CAN ARINC 825 - DO-254
Vendor
Vendor Name